82061 Neuried
- Gautinger Str. 45
82061 Neuried - +49 89 72481500
- info@dnpt.de
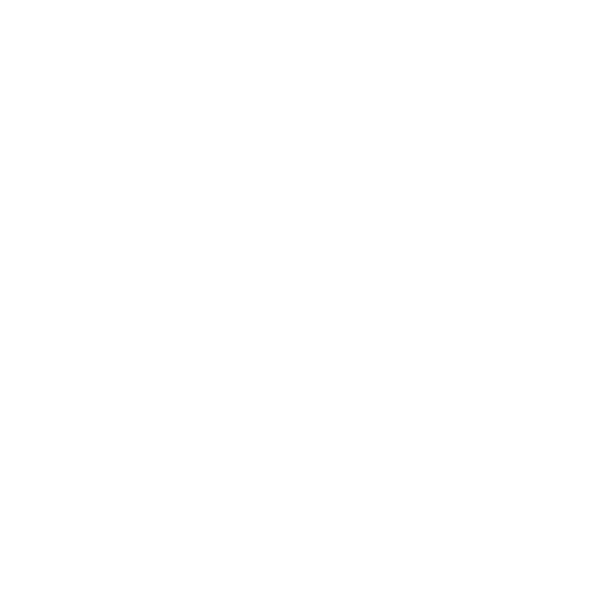
The trilateral transfer project “Spin-TEC”, which aims to temper high-precision motor spindles using advanced Peltier technology, is jointly conducted by the Fraunhofer IPM institutes and the Technical University of Berlin as well as application partners Fischer Spindle AG and Dr. Neumann Peltier-Technik GmbH (DNPT).
The goal of the Spin-TEC project is to improve the thermal stability & working accuracy of motor spindles through integrated Peltier tempering.
In precision machining of high-tech components, high demands are placed on shape accuracy: parts for medical technology, the aerospace industry, or toolmaking, for example, must be manufactured with submicrometer precision. The thermal behavior of the motor spindles in the machine tool plays a crucial role in the working accuracy of the machine. Electrical and mechanical losses of the motor and bearings cause heat flows, for example, to be induced into the shaft and housing of the spindles. This leads to rising temperatures and consequently to thermally induced deformations, which negatively affect working accuracy.
To date, long warm-up times are required to reach a thermally stable state of the spindle in the machine tool. Only in this way can manufacturing tolerances be maintained. Nevertheless, fluctuations in the induced heat flow and thus in the thermally induced displacement are unavoidable during operation, among other things due to tool and workpiece changes as well as adjustments of the spindle speed.
In the Spin-TEC project, the project partners are developing a novel, thermoelectrically tempered motor spindle. The core of the concept is tubular Peltier modules, which are integrated between heat sources and heat sinks, thus enabling controlled tempering of the bearings and the motor. This can increase the thermal stability of motor spindles and reduce their warm-up time compared to the state of the art. The thermoelectrically tempered motor spindle offers the potential to increase working accuracy and productivity of machining processes.
Particular advantages of tempering using Peltier technology include the possibilities in the field of miniaturization, the extremely high precision through corresponding controls, and the reversibility of cooling and heating operation. Precise tempering in the most compact form as intended by the project is only made possible through the use of Peltier technology.
Dr. Neumann Peltier-Technik as an experienced application partner of Peltier technology
Dr. Neumann Peltier-Technik GmbH provides extensive know-how and the necessary equipment for the implementation of the project. As a practical expert in the field of thermoelectric applications, practical knowledge in the field of Peltier technology can be incorporated into the project: Dr. Neumann Peltier-Technik supports the thermal design of thermoelectric components and the subsequent production of Peltier technology for integration into the motor spindle.
In addition, the associated control of the Peltier components is designed, and specially manufactured, high-precision, and compact controllers are provided. Special attention is paid to the high-quality requirements and the specifics of controlling Peltier technology and implementing various interfaces. The focus is already on the industrial application and networking capability of the application.
Project financing
The project is funded as a trilateral transfer project by the Fraunhofer-Gesellschaft and the German Research Foundation (DFG) (529738427).
Institute for Machine Tools and Factory Management IWF Technical University of Berlin
Dr. Neumann Peltier-Technik GmbH